Different elastomers
On construction sites, choosing the right materials is crucial to the success of a project. At UGA, we understand the requirements and challenges that our customers face on construction sites and therefore offer a wide range of elastomers.
We will now explain which elastomers we offer in conjunction with our products and where each one has its strengths! 🤗
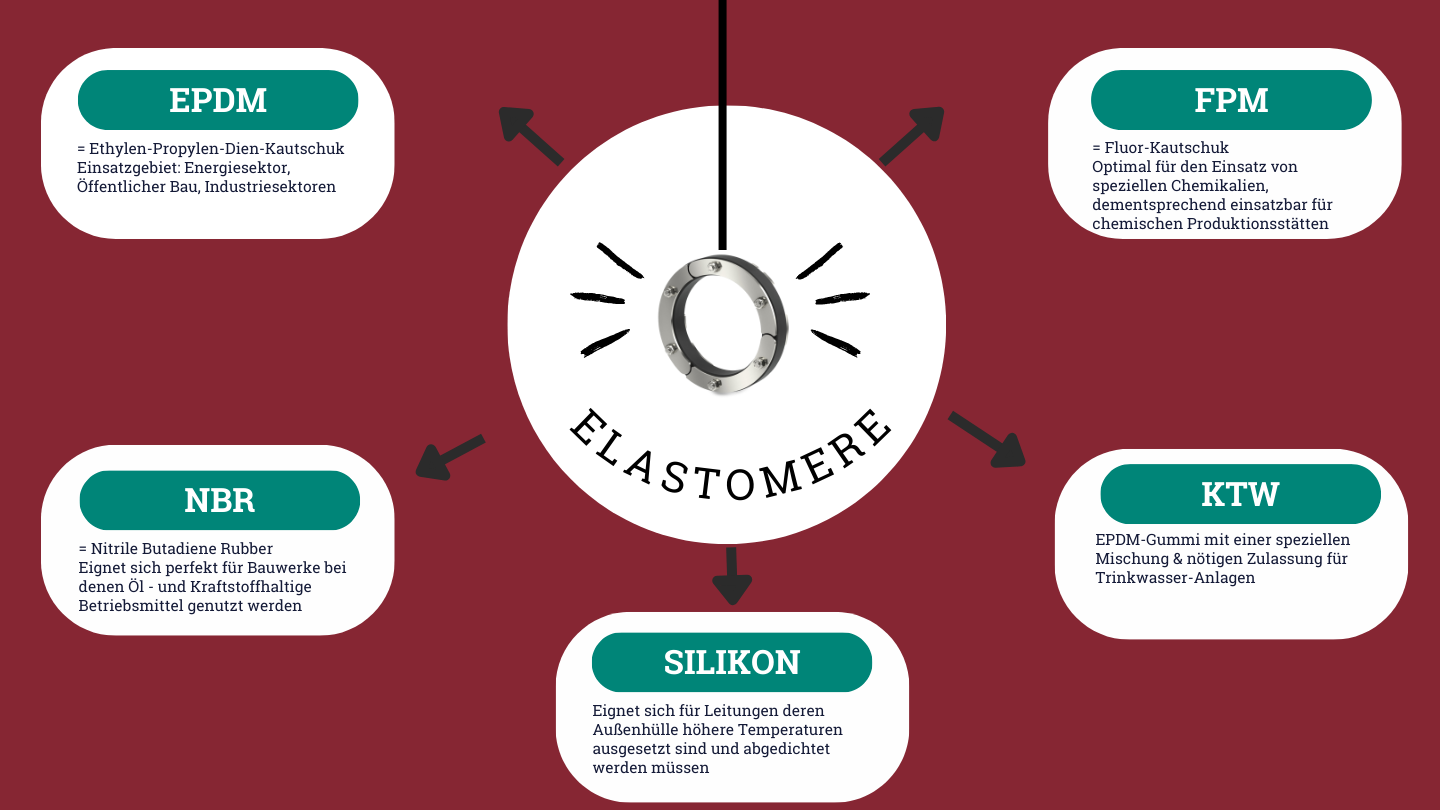
What are elastomers & where do we use them?
Elastomers are polymeric materials that can deform under the influence of external forces, but return to their original shape once the forces have been released. These elastomers are known for their elasticity and flexibility, which makes them ideal for use in our products. In our cases, we use a wide variety of elastomers in our products such as rubber press seals (GPD), ring-space seals (RRD) or system inserts, depending on the customer's wishes and requirements. For example, these elastomers, also known colloquially as rubbers, are pressed between the metal plates in our rubber press seals so that core drill holes or similar can be optimally sealed gas and water-tight.
What different elastomers do we offer?
EPDM: The classic, all-rounder!
Ethylene propylene diene rubber
- High resistance to ozone, UV radiation and ageing
- Resistant to acids and alkalis
- Withstands temperatures from -30 to +130 degrees Celsius
EPDM is the all-purpose weapon in the sealing sector due to the above-mentioned properties of the elastomer & the very good resistance to weathering/UV and various acids and alkaline environments.
Our field of application with EPDM is very broad. EPDM is used in the energy sector, such as substations, transformer stations, power plants of all kinds, onshore and offshore wind turbines. It is also used in public buildings such as hospitals, schools, public services or industrial sectors such as production facilities, research facilities or administrative buildings.
However, EPDM rubber is sensitive to petroleum, petrol, diesel, kerosene or propane (gas), which makes EPDM unsuitable for petrol stations, for example.
NBR:
Nitrile Butadiene Rubber
- Outstanding mechanical properties
- High abrasion resistance, high tear and tensile strength, low compression set
- Chemical resistance to Alcohols, fats & oils, acids & alkalis, mineral oil, fuels, aliphatic hydrocarbons, silicone oil & grease
Due to these chemical resistances, NBR is ideal for all structures in which oil and fuel-containing operating materials are used, such as filling stations, decanting systems or chemical plants.
Silicone:
- Good resistance to heat, ozone and ageing
- Good resistance to chemicals
- Unchanged mechanical properties over the entire temperature range from 60 to 180 degrees Celsius
We use silicone when pipes need to be sealed that have higher temperatures on the outer shell. This means district heating, industrial and chemical production facilities or research facilities.
FPM:
Fluororubber
High penetration resistance (good electronic insulators)
Very abrasion resistant
Ideal for high temperatures up to 200 degrees Celsius
Very resistant to tearing
Excellent resistance to acids, alkalis, aliphatic, alkaline aromatic and halogenated hydrocarbons
Resistant to fuels, which do not cause FPM to swell even after long-term exposure
However, FPM is susceptible to water vapor, alcohols and polar solvents! FPM rubber has low gas permeability and becomes brittle at temperatures of -20 degrees Celsius.
This is why we mainly use this rubber in chemical production facilities or research institutes.
KTW rubber: Our EPDM with extra testing for drinking water!
KTW rubber is basically our EPDM rubber with a special material mixture that enables us to use it for drinking water systems in accordance with certain DIN standards. Certain approvals are required for this, which we can provide!